Control Engineering: Using a 3D digital twin and augmented reality
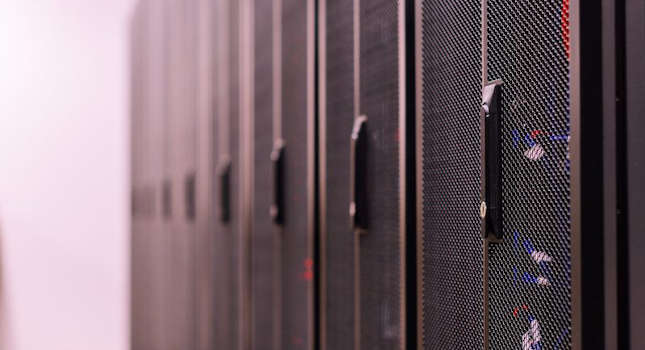
3D digital twins and augmented reality (AR) can help manufacturers better understand places that are often dangerous for a human to access.
A digital twin is a digital replica of a physical device. The session at ARC Industry Forum “Digital Twins for Improving Operations and Maintenance” provided an explanation of the types of digital twins in industry and their applications. During plant design and build, a “project digital twin” provides a means to simulate and improve front-end engineering design (FEED), construction sequencing and commissioning.
For operations, the performance twin uses real-time data to assess status for predictive maintenance, process optimization, and operator training. A 3D digital twin of a plant can also be used to navigate to a virtual representation of an asset to access information about the real asset, which is the topic of this case story.
Digital twin for off-site operations support
During ARC Forum session exploring digital twins in plants, CEO and Managing Director of Delta Drone International Christopher Clark presented his company’s approach to digital twins. This presentation provides a user case story by Rocketmine, a subsidiary of Delta Drone Group, for the application of a digital twin using Bentley Systems’ PlantSight software.
Plantwide asset information with remote access
Using a combination of laser scans and photogrammetry, Rocketmine created a 3D model of a mine processing plant. During the ARC Virtual Forum, Delta Drone presented its case story for plant support by off-site experts using:
- 3D digital twin for current information
- Augmented reality to guide in real-time.
The need for remote access accelerated during the pandemic. Benefits include faster time to issue resolution with no travel time.
Important assets are converted into a software object. Links to sources of information for that asset are added to the object. A user of the Bentley software can navigate through the 3D model to the asset, double click on the software object, and obtain current, federated information about the asset.
Remote plant access with augmented reality
With the COVID-19 pandemic, plant operators need a means to obtain support from people not able to enter the plant. This is where augmented reality (AR) comes in. A remote expert can see what a person in the plant sees and give them guidance. The expert can draw notations onto the display that both see. With HoloLens’ integrated 3D scanning capability, the notations remain fixed where they were drawn relative to the real objects in view – even when the person moves their head.
The software for the remote expert scenario comes with HoloLens. The on-site person will likely need the integrated hardhat. The remote expert can use an office grade Microsoft HoloLens device.
Co-presenter Devon Hasenbroek demonstrated augmented reality (AR) by stepping through a previously written instruction sequence for changing the battery in a drone as an example of AR being used to aid people in performing important procedures with which they are not familiar. Hasenbroek and Clark also demonstrated the remote expert scenario.
AR offers a means for collaboration to solve a problem that the person in the plant is not familiar with. Many companies have experts in a central location supporting multiple plants. Using AR avoids travel with faster time to resolution and reduced travel costs. Payback often occurs in months. Users should consider AR for real-time support of plant personnel by remote experts.
Ralph Rio, vice president, enterprise software, ARC Advisory Group. Edited by Chris Vavra, web content manager, Control Engineering, CFE Media and Technology, cvavra@cfemedia.com.
Original article: https://www.controleng.com/articles/using-a-3d-digital-twin-and-augmented-reality/